Metal fume fever is a potentially fatal form of hazardous materials exposure where people inhale toxic fumes from heated metals. Not all metals can cause this condition and galvanized metals are the most likely culprits. Patients inhale magnesium oxide and zinc oxide, both known respiratory irritants, and can develop serious illnesses. While many people recover after mild exposure, the episode can put them at increased risk of respiratory infections like pneumonia.
People develop metal fume fever when they work in poorly ventilated environments with metals they are heating for projects. Furnaces, welding kits, and soldering kits can all expose people to hazardous fumes. It is important to use hood ventilation over workspaces to trap and vent fumes, to make sure metalworking facilities have good cross ventilation, and to wear respirators and face shields as appropriate. Even low level exposure can make people very sick.
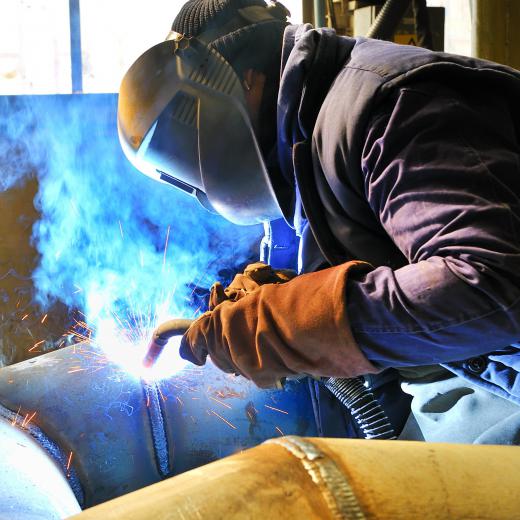
A patient with a single incident of metal fume fever will develop chills, nausea, sweating, vomiting, and joint pain. Some patients report a metallic taste in their mouths, chest pain, changes in urinary output, and an unusually high white blood cell count. A blood test can reveal abnormally high concentrations of metals in the blood. Repeat episodes can make people prone to serious respiratory problems like asthma and lung infections.
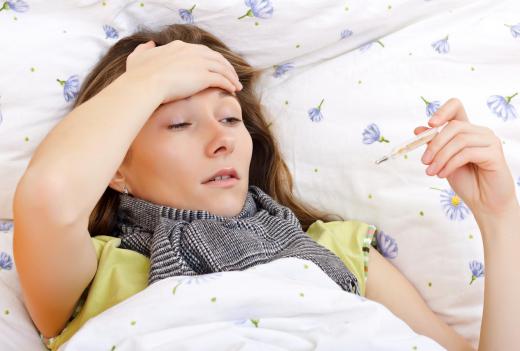
Typical treatment for this occupational illness is resting in bed, drinking lots of fluids, and taking medications like aspirin to treat symptoms. Patients can recover in two to four days from metal fume fever. When they return to work, it is important to limit exposure to metal fumes, because they can be more vulnerable to future episodes of illness. People with a life-long history of working in poorly ventilated environments may experience metal fume fever regularly, and could develop severe health complications.
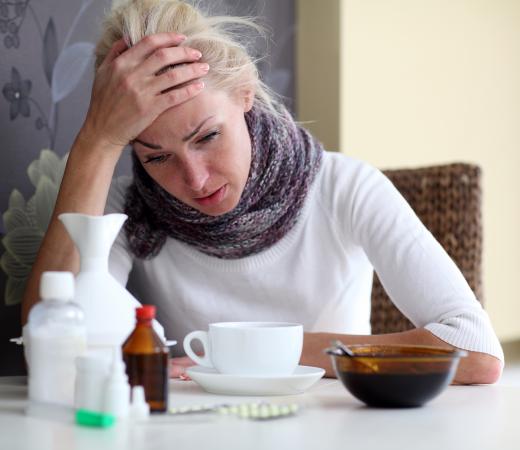
Workplace safety laws require measures like proper ventilation and respiratory protection for workers. Supervisors need to make sure their personnel abide by the laws even if equipment is uncomfortable or heavy, and should regularly check ventilation systems to confirm they are functioning properly. It is important to train new employees and to have a safety officer who can periodically check up on working conditions. People running their own shops and working alone should be careful when working with hazardous materials, as they may become dizzy and lightheaded if they are exposed to toxins. This could make it hard for them to take appropriate action to protect themselves.